The operation of the HL-LHC IT String will mark a significant milestone for the High-Luminosity LHC (HL-LHC) project, as many state-of-the-art technologies developed for the HL-LHC will work collectively for the first time.
In the last episode of the HL-LHC IT String, featured in Accelerating News, we highlighted the completion of infrastructure installations for the test stand and the readiness of some equipment to be commissioned.
Let’s have a look at the advancements occurred since then!
Installations
After the placement of the power converters chassis on the IT String metallic platform, the teams of SY-EPC / WP6b proceeded to finalise their configuration by installing the power modules, control electronics and the current measurement sensors, all essential components for energising the circuits.
The installation of CLIQ racks by TE-MPE/WP7 at their final position in the IT String area also marked a significant advancement. The CLIQ system is an innovative active protection mechanism that safeguards the magnets from damage in the event of quenches.
Additionally, the integration of copper-made, water-cooled busbars (WCBB) constituted another leap in the installation phase. These busbars facilitate the transmission of current from the 14 kA and 18 kA Circuit Disconnector Boxes (CDBs) to the DFHX, a crucial component of the cold powering equipment that serves as a warm-to-cold feedbox.
Furthermore, a mock-up of the DFHX was installed on the IT String platform by TE-MPE/ WP16 that mirrors the essential dimensions of the actual DFHX. This approach was adopted to facilitate the preliminary installation of the air-cooled cables and busbars (see Fig. 2) and the execution of short circuit tests, which are crucial in the final phase of the warm powering equipment commissioning. This setup ensures that, upon delivery of the real DFHX, it can be integrated into the existing framework without major adjustments.
Another important event was the execution of the final major control cabling campaign, by EN-EL teams, which involved the installation of approximately 250 cables. This task not only encompassed the laying down of these cables but also included the fitting of cable connectors and the performance of a final continuity test to ensure integrity. Numerous control systems related to machine protection, survey and alignment - and the cold powering system – rely on these cables.

Commissioning
Following the installation phase, the hardware commissioning of equipment related to the warm part of the circuits was executed in two primary stages: Individual System Tests (IST) and Short Circuit Tests (SCT).
The IST involved a series of checks on each piece of equipment, conducted in isolated from the rest of the circuit, to validate its functionality. This testing was executed in a variety of equipment, including the power converters (PCs), energy extraction systems (EEs), Circuit Disconnector Boxes (CDBs), Power Interlock Controller (PIC), Water-Cooled Cables (WCC), Air-Cooled Cables (ACC), and Water-Cooled Busbars (WCBB). All these tests were successfully completed and documented within the String Quality system. Additionally, on the request of the equipment owners and/or the coordination team, safety audits by HSE or external companies were conducted and successfully passed, qualifying the circuits’ connection to the electrical network of CERN.
The ISTs were followed by the SCT in each of the circuits. These tests are crucial for validating that the different elements of the circuit can work altogether as foreseen by the design. Current was injected into the circuits, allowing the evaluation of the different control and protection loops. Thermal performance was also scrutinised by monitoring various spot temperatures to localise any potential overheating in connections, equipment or infrastructure.
All these tests required careful coordination with other ongoing activities to ensure not only efficiency but also safety. Adequate safety measures were implemented, including access control via IMPACT, allowing various teams to engage with the equipment in accordance with its operational status. This was imperative as the equipment on the IT String platform was already energised, and current was being circulated through the circuits during these tests.
The commissioning phase for the Cryogenic Distribution Line (SQXL) advanced significantly, encompassing up to two cooling phases under cryogenic conditions in 2023. These phases allowed for the mechanical and thermal validation of the system, ensuring it functions as designed. Subsequent efforts are being focused on control loop tuning, aimed at optimising performance and achieving precise control over the cryogenic processes during a scheduled run in 2024. Additionally, thorough checks and corrections were conducted to ensure the integrity of the line's vacuum system, further guaranteeing the operational readiness of the SQXL.
Upcoming challenges
As the installation phase progresses, several challenges that require careful consideration lie ahead. A particularly significant challenge in 2024 involves the installation of the cold powering system. This complex operation will entail the coordinated lifting of the DFXH and ScLink to the IT String metallic platform using two cranes simultaneously, along with ad-hoc lifting ancillaries. This manoeuvre, crucial for the progress of the project, is being meticulously prepared in SM18 building (see Fig. 3).
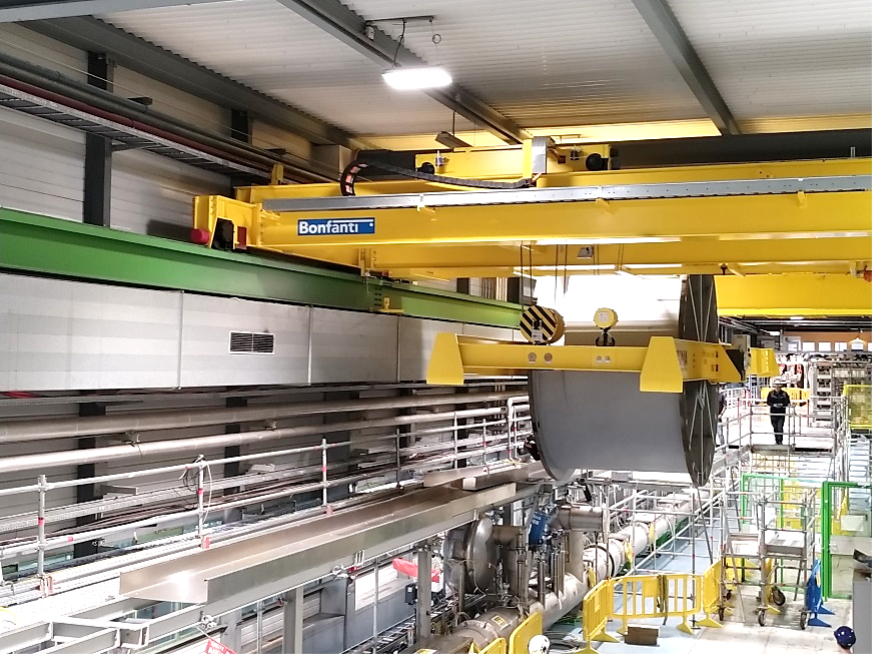
Following this, more activities linked to the cold powering system are scheduled, including the assembly of the DFX cold feedbox and the insertion of the ScLink into it.
In September, the installation of jacks and anchors, integral components of the alignment system, is planned. These elements are necessary for accurately positioning the magnets. The magnets themselves are to be installed in their final positions immediately following the placement of the jacks, marking a year filled with intricate installations.
The start of operation for the entire test stand in nominal conditions is approaching... More updates will follow, so stay tuned!